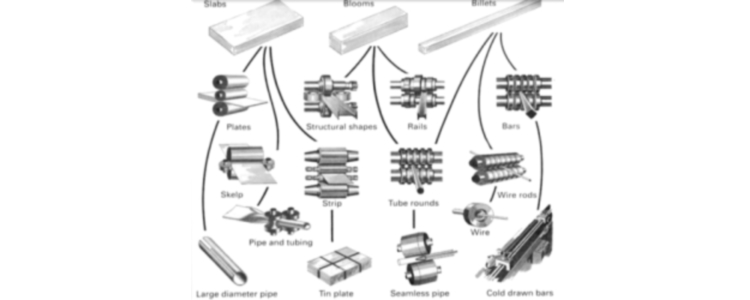
Hot Forming
In the blog before we spoke on cold working process which refers to strengthening of metal by plastic deformation at normal temperatures. In contrast, hot working refers to process where metals undergo plastic deformation at temperatures above their recrystallization point. This helps achieve the material to recrystallise during deformation. This is essential as recrystallization prevents the material from strain hardening, thereby preserving the yield-strength and low hardness along with high ductility of the material. This differentiates hot working from cold working.
Temperature for Hot Working:
The lower limit for hot working is determined on basis of its recrystallization temperature which is generally 0.6 times of it melting point on an absolute temperature scale. On other hand, upper limit for hot working depends on numerous factors including grain growth, excessive oxidation or an undesirable phase transformation. While hot forming, materials are generally heated to upper limits to minimize forces as well to gain maximum time to hot work the workpiece.
However after attaining the desired hot forming temperature it is equally essential to maintain this temperature. Most of the heat during heat forming is lost through surface of workpiece to cooler tooling around. This causes temperature gradients in workpiece which can lead to cracking in the cooler, lesser ductile surfaces. Hence, in majority of cases tooling is heated. Hotter the tooling, lesser would the heat be lost. Keeping all these conditions in consideration, ideally hot working is performed around 325-450C. The lower limit for hot working for tin is room temperature whereas is 2000F for steel and 4000F for tungsten.
Some major hot forming processes include:
The main advantages of hot forming are as follows:
- The process is very economical as lower working forces are required to produce shape change owing to heat involved, thereby needing no involvement of strong machinery.
- It process a dramatic change in shape in single working step without causing huge internal stress, cracks or cold working.
- It can be carried out simultaneously with casting processes thereby getting the metal cast and instantaneously worked hot. Thus, being much economical saving time and money for reheating the work piece.
- During hot working while recrystallization, large crystals are broken producing a favorable alignment of crystals.
- In certain cases, hot working can help remove defects in cast metals. For example sometimes gas pockets are developed in case billets or it can help break non-metallic slag or inclusions which can caught in the melt.
- Hot forming replaces the basic microstructure of the material with fine spherical shaped grains, thereby enhancing its engineering properties increasing its strength, ductility and toughness.
Even hot forming has some disadvantages, making end-result requirement as a decisive factor to choose between hot forming and cold working. Some of the major disadvantages are as follows:
- Sometimes hot forming can be very uneconomical owing to involvement of ostly equipment like gas or diesel furnace or induction heater.
- Sometimes undesirable reactions occur between the material and surrounding environment leading to scaling or rapid oxidation of material.
- In certain cases, there can be uneven grain structure throughout metal for various reasons.
- Uneven cooling can cause lesser precise tolerances.
This entry was posted on Monday, February 17th, 2014 at 5:12 pm and is belong to category Blog.