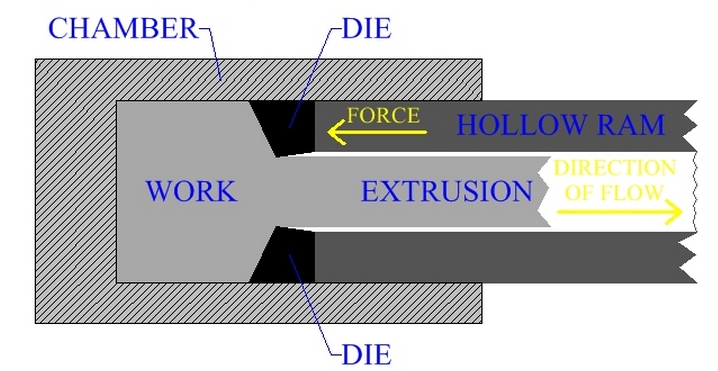
Indirect or Backward Extrusion
In the previous blog on Direct Extrusion, we had pointed the main disadvantage of direct extrusion being the excess use of force due to friction between the cylinder and billet. Accordingly, to deal with this issue, whenever possible one can use indirect or backward extrusion, wherein comparative lesser force is required for extruding the material.
Indirect or backward extrusion is a type of metal extrusion process wherein the billet(work-piece) is kept inside the chamber, which is completely closed on one side. In this type of extrusion, the billet and the container move simultaneously whereas the die remains stationery. Extrusion dies are placed on the ram, which applies the force from the open end of the chamber. These dies are held tightly in position by the “stem” which is longer then the length of the container. The column length of this stem decided the ultimate length of the extruded metal.
As the extrusion process continues, the extruded product flows in the direction opposite to that of the ram. Accordingly, the ram is kept hollow at the centre so that the extruded section of the billet can travel through the ram itself. Thus, the material flows in backward direction as compared to the direction of the ram and hence the name “backward extrusion”.
Indirect extrusion, can be used for manufacturing hollow parts as well. For hollow kind of extrusion, ram is forced into the billet, which gives internal geometry to tubular part, whereas forming material around it. However, difficulties in supporting the ram limit this kind of tubular metal extrusion and also limit the length of such extrusions.
In Indirect or backward Extrusion, the billet remains stationery inside the chamber, thereby producing no frictional force. Also, the extrusion pressure is not affected by the length. This leads to following advantages of indirect extrusion:
- There is a reduction of nearly 25-30% in the frictional forces, thereby allowing larger billet-extrusion, increased speed of extrusion as well as an increase in capacity to produce smaller cross-sections.
- With lesser friction, there is comparatively lesser heat developed, leading to reduced possibility of extrusion cracking.
- The chamber has longer life due to lesser wear with lesser friction as well as heat.
- Since the billet is extruded more uniformly, there are relatively lesser extrusion defects and less chances of formation of coarse grained peripherals zones.
Amongst all these advantages, there are certain disadvantages as well which one cannot ignore as follows:
- The surface of the extruded material is badly affected sometimes by the defects as well as impurities of the billet. Incase there is a need to anodize or if the aesthetics are important, these defects can ruin the extruded piece. These issues can be taken care by wire-brushing, or by cleaning the billet before being extruded.
- The length of the extruded material is limited by the length of the stem, thereby limiting the versatility of the process as compared to direct extrusion.
Bharat Industries with its 40 years of experience in Extrusion Process along with its extensive process understanding and system competence of our specialists, can provide you high-quality extrusion dies to achieve utmost results in indirect extrusion.
This entry was posted on Tuesday, December 10th, 2013 at 9:09 pm and is belong to category Blog.